Lupine Publishers| Journal of Civil Engineering and its Architecture
Abstract
Manufacturing of fly-ash bricks are the very useful alternatives of conventional burnt clay bricks. Manufacturing of clay bricks cause top soil removal, environmental pollution and health problems. To avoid all this environmental threats an attempt is made to manufacture of bricks using fly-ash, gypsum, sand and cement. Mainly fly-ash bricks are made by applying compressive load on the mold. In this research, the effect of brick forming load on the crushing load, water absorption and unit volume weight were studied. For this purpose bricks were prepared for different fly-ash (50% to 65% at 5% increments), gypsum (12% to 3% at 3% decrements), sand (28% to 22% at 2% decrements) and 10% cement. All ingredients were thoroughly mixed and then poured them to a mold of 9.5cm x 4.5cm x 2.75cm. Bricks were made by different forming load and mechanical properties were noted. This research suggested that it was possible to make good quality bricks using fly-ash, gypsum, sand and cement.
Keywords: Fly-ash; Gypsum; Sand; Cement; Brick forming load; Mechanical properties
Abbreviations: IS: Indian Standard
Introduction
Fly-ash is a predominantly inorganic residue obtained from the flue gases of furnaces at pulverized coal power plants. Fly-ash is produced in a large scale in all over the world. Production of fly-ash in different countries [1] is shown in Figure 1.
Now it has become a concern to dispose it in a right manner. For this many researchers have tried to found out the way to use them. Fly-ash is now used in different sectors like brick making, agriculture, concrete production, embankments, road pavement, mineral filler in asphaltic concrete, mine reclamation etc. Recent review such as [2,3] presented the possible applications of fly-ash. Fly-ash is now used in agriculture to increase the land properties [4]. Fly-ash has cementious properties. Thus, it has been used in making concrete [5]. Now fly-ash is disposed in the form of bricks. These bricks are made commercially in many countries like United Kingdom, Germany and India. Many solidifying agents are used in production of fly-ash bricks like lime [6], slag [7,8], dextrin [9] and gypsum [10,11]. Several numbers of patents on the use of fly-ash-lime mixures to make unfired bricks [12-15]. Gypsum is an important by-product of fertilizer industry and causes serious environmental problem [16]. The strength of fly ash-lime-gypsum (FaL-G) bricks and hollow blocks increased at a faster rate in initial days of curing and subsequently at a relatively lower rate. It was observed that the hot water curing leads to a greater degree of hardening and higher strength. Water absorption increases with increased fly ash content and it decreases with an increase in the density of FaL-G bricks and hollow blocks [17]. The strength of concrete increased with increasing amount of fly ash up to an optimum value and decreased with further addition of fly ash. The optimum value of fly ash for the test groups is about 40% of cement. Fly ash/cement ratio is an important factor determining the efficiency of fly ash [18]. The phenomenon of bond development between the fly ash-lime-gypsum (FaL-G) brick and the mortar. The morphological and microstructure studies of the brick-mortar interfaces clearly proved the chemical bond formation at the FaL-G brick-mortar interface [19]. The effect of incorporating various additives (i.e. cured resin, pulverized stone, pulverized plaster, and glass fibers) and two drying method (air and microwave) on compressive strength of gypsum products. Microwave drying for 5 minutes could fasten the drying time and permit early manipulation of plaster and stone models [20]. The addition of fly ash enhanced the quality of the brick, although for restoration purposes if too much fly ash (P10 wt.%) is added, this can spoil the aesthetic appearance of the buildings being restored, due to excessive color differences [21]. The replacement of raw materials of clay by fly ash to make fired bricks is an effectively measure of saving land and decreasing pollution. The sintering temperature of bricks with high replacing ratio of clay by fly ash was about 1050C, which was 50-100C higher than that of fired clay bricks. The fired bricks were of high compressive strength, no cracking, low water absorption, high fastness to efflorescence, no frost and high resistance to frost-melting [22]. A technique for producing concrete bricks and paving blocks using C&D wastes as recycled aggregates. The replacement of coarse and fine natural aggregates by recycled aggregates at the levels of 25% and 50% had little effect on the compressive strength of the bricks and blocks, but higher levels of replacement reduced the compressive strength [23]. The investigation of industrial wastes produced by phosphoric acid plants and boron concentrators was used in light brick production. The environmental need to utilize wastes that would be hazardous otherwise. The economy of possible use of these wastes is also of importance since the disposal of the wastes [24]. Fly-ash-gypsum bricks are used as a lightweight, heavy strength and low cost bricks. Reaction of gypsum are taken place in the presence of water. By the presence of water it forms crystalline material which is not strong enough to bear a good compressive strength but uses as a finishing materials. In the past fly-ash was released to environment. Fly ash is used as pozzolan to produce cement. Fly-ash with gypsum is made a tough material having good finishing.
Experimental Programme
Materials used
Fly-ash: Fly ash used in this research was collected from Noapara, Jessore which is imported from India. Specific gravity of fly-ash was 2.10. The chemical compositions of fly ash in India [25] are indicated in Table 1.
Gypsum: Chemically known as “Calcium sulphate hydrate”. This material is non-toxic and don’t create any harmful effect on the human body, environment, plant lifes and animals. Gypsum used in this research was collected from Noapara, Jessore. Specific gravity of gypsum was 2.34. The chemical compositions of natural gypsum [10] is indicated in Table 2.
Table 2: Chemical composition of natural gypsum.
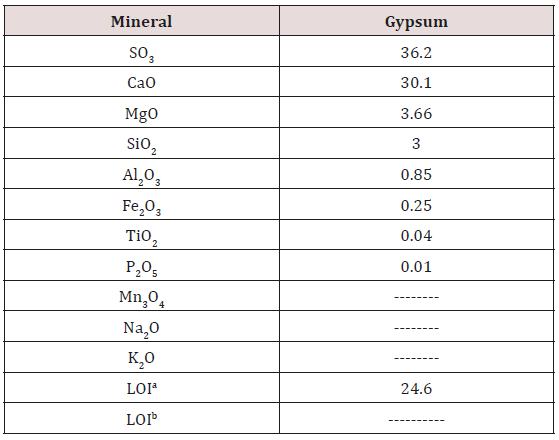
aLoss of ignition at 950 °C
bLoss of ignition at 550 °C
Sand: Locally available sand were used in this study. The specific gravity of sand was 2.78 and fineness modulus was 2.34.
Cement: Cement is a binder, a substance used for construction that sets, hardens and adheres to other materials, binding them together. Ordinary Portland Cement was used in this study. The physical properties used are given in Table 3.
Proportion and mixing of raw materials: Different proportion are used to cast fly-ash bricks. Materials are used as a percentage of the volume of the mold. Percentage of materials required for fly-ash bricks and brick no. for each proportion in different curing process and curing period Table 4.
Table 4: Percentage of materials required for fly-ash bricks and brick no. for each proportion in different curing process and curing period.
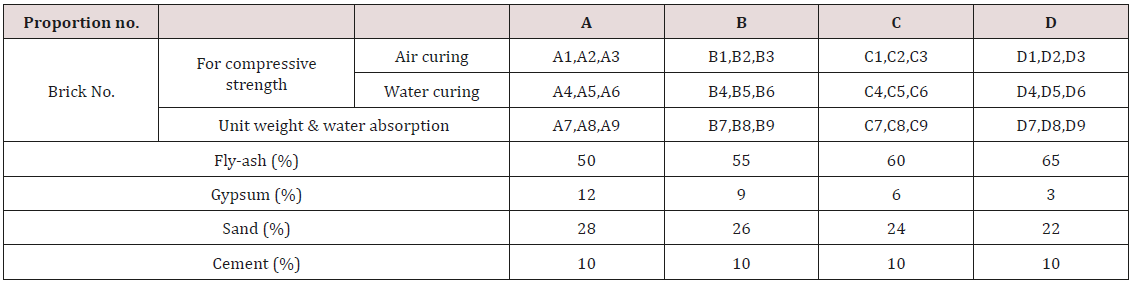
The amount of ingredients was weighted then mixed thoroughly in a dry state. When the colour of the mixed was seemed to uniform then water was added. After addition of the required quantity of water the mixture was thoroughly mixed in a pan. The water content used in this study was 80ml. The mixture was again thoroughly mixed until the mixture attained a uniform consistency.
Preparation of mortar blocks
A brick mold of size 9.5cm x 4.5cm x 2.75cm was used in this study. Then the mortar was placed on the mold and compacted using digitec concrete compression machine. The load was applied with average time of 15 seconds to 20 seconds. Then the excess mortar was hand finished. Nine specimens were prepared for each proportion. After that the brick forming load from the screen of the digitec concrete compression machine was recorded.
Curing of brick sample: The brick sample was taken out from the mold after 10 minutes. After removal from the molds, the brick samples were kept for air drying for 2 days. After sufficient strength was gained some of these bricks were transferred to water for 14 days and others were kept in air.
Method of testing: Poping out from the water bowl after 14 days curing, bricks were tested for compressive strength using digitec concrete compression machine. Compressive strength and water absorption test were conducted by following IS:3495 [26] and unit volume weight was conducted using literature.
Results and Discussion
Effect of brick forming load on crushing load
Air curing: Table 5 gives the information of forming and crushing load on water curing fly-ash bricks while Figure 2 presents the graphical representation of table 5. In Figure 2, crushing load is experienced upward in the first and gradually decreasing to the last. On the other hand forming load is gradually upward. Brick No. A3 gives the highest crushing value from all the available bricks which is marked in the Table 5 while C1 shows lowest crushing value.
Water curing: Table 6 illustrates the forming load as well as crushing of fly-ash bricks of water curing of 12 bricks while Figure 3 represent the graphical demonstration of Table 6. Figure 3 shows a variety of deflections in crushing load of fly-ash bricks. Brick No. A3 gives the maximum crushing value i.e., 62.5kN and D5 shows the lowest crushing value of about 31.28kN shown in Table 6. Both values are highlighted to visualize easily with graphical representation.
Effect of brick forming load on water absorption: Table 7 depicts the variation of water absorption in accordance with the brick forming load in a tabular format and with the help of these data a graph was plotted to easy visualization (Figure 4). Marked B9 and C7 shows lowest and highest water absorption respectively. The bar diagram shows almost same variations which is indicated in the Figure 4.
Effect of brick forming load on unit volume weight: Experimental data on conducting research on fly-ash bricks have been illustrated in a table format in Table 8 and a bar graph (Figure 5) was used to show the variation unit volume weight with the brick forming load. Though forming loads show a variations but unit volume weight seems like a plain straight.
Conclusion
Usually, FA obtained high strength at the initial stage of the formation of fly ash bricks while FA need long term hydration for the FA. In this study, it is found that crushing load for the water curing is higher at the brick no. of A6 shown in the Table 6. For considering the air curing into account, and displayed maximum crushing load for the brick A3 shown in Table 5 and by bar diagram in Figure 2. The maximum crushing load for air and water curing for fly-ash bricks were 76 and 62.5kN respectively while minimum crushing load were 41.25 and 31.28kN for air and water curing respectively. By performing the comparison between air and water curing, an interesting outcome is found that crushing load for air is greater than the crushing load for water curing. It may be happened due to initial hydration effect of fly ash.
By taking water absorption, it is shown in Table 7 along with the Figure 4 that B9 and C7 gives the maximum and minimum water absorption respectively. Looking to the other bricks demonstrates almost same fluctuations of water absorption. Almost same results were found also in the unit weight of the fly ash bricks in which the results (Figure 5) displays the same height at the forming load.
By doing the study, it may be concluded that proportion for brick “A” is quite good rather than other bricks. More research should be conducted on fly ash bricks to attain more accurate results and relationship.
Read More About Lupine Publishers Journal of Civil Engineering and its Architecture Please Click on Below Link: https://lupinepublishers-civilengineering.blogspot.com/
No comments:
Post a Comment
Note: only a member of this blog may post a comment.