Lupine Publishers| Journal of Biomedical Engineering and Biosciences
Abstract
In recent years, many studies on magnesium (Mg) alloys are focused on developing biodegradable medical implant. Interests are also placed upon the implant geometry related to corrosion processes. In this study, a simulation model to analyze pitting corrosion of Mg alloys is established with a Monte Carlo procedure. The Mg specimen is meshed with uniform hexahedral micro elements. Each element can be characterized by a corrosion probability (CP) for a time interval. The CP value is based on factors such as the number of surfaces exposed to the solution, properties of oxide layer, the porous structure and the Mg matrix. The results are compared with experimental measurement using a micro computed tomography (CT). The computational model appears to be useful for long-term simulation and analysis of corrosion behaviors and prediction for biodegradable implant development.
Keywords: Magnesium Alloy; Micro-CT; Monte Carlo Method; Pitting Corrosion simulation
Abbrevations: Mg: Magnesium; CPi: Corrosion Probability; EAi: Expose Attribute; OAi: Oxide Attribute; CAi : Corrosion Attribute; Micro-CT : Micro Computed Tomography
Introduction
Biodegradable magnesium (Mg) alloys were investigated in recent years by many investigators for developing medical device. One of the tasks is to match corrosion rate with tissue regeneration which is a long term growth. The present study is to develop a computational procedure simulating corrosion processes. The Mgspecimen is modeled as hexahedral elements of 125 microns in size. Each element is in contact with adjacent elements or saline. The corrosion probability (CPi) for an element is determined at each time step. In this study, CPi was considered with two factors: the expose attribute (EAi) and oxide attribute (OAi). The number of element surfaces in contact with saline is indicated by EAi. As the oxide magnesium surface is much slower in corrosion than the intact magnesium, the material characteristics are represented by OAi. The combined effect is expressed as the corrosion attribute indicated by CAi= EAi* OAi. In the computational analysis, the corrosion rate is based on experimental data of magnesium mass loss obtained by a micro-CT every 25 hours for a period of 500 hrs. The corrosion probability of an element is
In which MLis mass loss of specimen, Me the mass per element, and Σni=1 the total corrosion attribute of all the elements. The inhomogeneous property on the oxide layer could lead to pit corrosion [1,2]. Initially, the Mg specimen surface was a protective oxide layer. When the porous reign of oxide layer was corroded by saline, the Mg alloys matrix inside became exposed and its corrosion rate was much faster than oxide layer, resulting in pitting corrosion. In this study, the setting of three OA values were based on the corrosion rate calculated from the data of electrochemical corrosion tests [3-6] by classic Tafel analysis [7]. The Monte Carlo procedure was applied to determine which elements to be corroded in a time step.
Figure 1 shows the overall comparison of the corrosion simulation and experiment at different time: 50h, 100h and 250h. While the mass loss rate of the simulation is based on the experimental data, the corrosion patterns are related to the characteristic micro-structure of oxide layer. Figure 2 compares a corrosion simulation of the specimen surface with two inner sections at 0.125 mm apart. Similar patterns on these three layers show the development of pitting corrosion from surface to the mid-section, and from corrosion time of 100h to 300h and 500 h. Because the in homogeneity of oxide top and bottom surfaces are not the same, pitting patterns on the lower half specimen are somewhat different.
Figure 1: Overall comparison of the corrosion simulation and experiment.
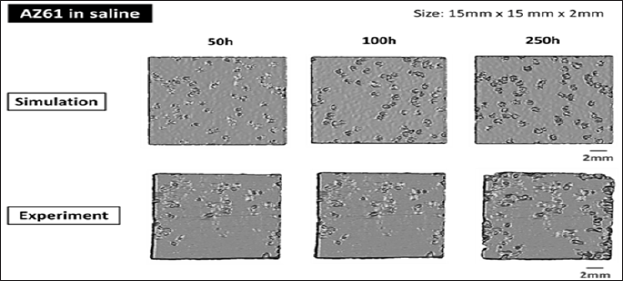
Figure 2: Corrosion simulation of a magnesium alloy; z = 0 mm for the surface and z = 0.25 mm.
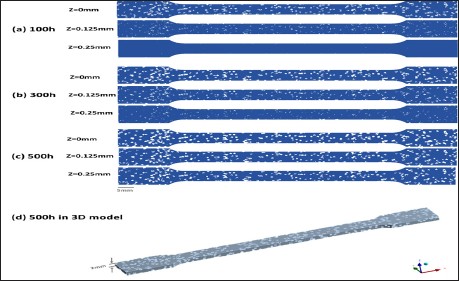
Conclusion
The characteristic micro-structure of oxide layer is a dominant factor for corrosion simulation. The quantification of 3D images by micro-CT is useful for comparing experimental results with the simulation. The computational model for the corrosion of magnesium alloy showed a good agreement with experimental results of 500 hours. The computational model appears to be useful for long-term simulation and analysis of corrosion behaviors and prediction for biodegradable implant development.
Read More About Lupine Publishers Journal of Biomedical Engineering and Biosciences Please Click on Below Link: https://biomedical-sciences-lupine-publishers.blogspot.com/
No comments:
Post a Comment
Note: only a member of this blog may post a comment.