Lupine Publishers | Journal of Textile and Fashion Designing
Abstract
Introduction
Pectin is used in a number of foods as gelling agent in jam and jellies, thickener, texturizer, emulsifier and stabilizer in dairy products, fruits preparations or in icings and frostings. It is also used in pharmaceutical, dental and cosmetic industries for its jellifying properties. It is generally produced by acid extraction of citrus peel followed by filtration and precipitation by alcohol as 2-propanol [3]. There are three different extraction techniques of pectin from citrus peels; acid hydrolysis, enzymatic and water extraction methods. Compared with acid hydrolysis, enzymes extraction of pectin is preferred despite of its cost because only a little effluent in the filtrate and because of consumer demands for green products. However, the mechanism of enzymatic extraction is still not fully understood [4]. Water soluble pectins inside the plant cell wall of plants can be easily extracted with boiling water. Although it is conventional and the easiest means of extracting pectin, this method is not applicable for commercial extraction of pectin because longer time and elevated temperature is required to isolate adequate pectin from the peels. Boiling the peels at elevated temperature for long time cause degradation of the pectin during extraction and is relatively costly because of the high energy requirement [5].
In this study, acid hydrolysis of pectin using HCL and H2SO4, new Pectin extraction method using sodium carbonate and Conversion of pectin into sodium pectate for textile reactive printing paste thickener application was investigated. The advantages of sodium pectate as thickener than using sodium alginate is also shown with comparative study of the thickeners in terms of color yield, wash fastness and color brightness.
Materials and Methods
Methods Materials, Equipments and Chemicals
The materials used for this study were 100% cotton full bleached woven fabric, Dried Citrus Fruit peels, 8 scale gray staining and color change scale. Beaker was used to boil the mixture of citrus fruit peel, water and acid, stirring spoon, and thermo meter to control the extraction temperature, weighing balance for weighing the amount of chemicals and materials used for the extraction of Pectin, PH meter to control extraction PH, launder-meter for wash fastness testing, mini dryer to dry and cure printed fabric sample and spectrophotometer to measure k/s value of the printed area [6-10].H2SO4, HCL and Na2CO3 were used to extract pectin from citrus peels so were used. The solvents used to precipitate pectin were ethanol, methanol and acetone. For the conversion of pectin into sodium pectate, isopropyl alcohol, NaOH and common salt are used. Isopropyl alcohol is used to wash the pectate and common salt is used to solidify the derived sodium pectate. The chemicals used to print cotton fabric were Sodium alginate as a thickener, sodium carbonate as dye fixing agent, Dispersing agent to form true solution of dye paste, Urea to prevent hygroscopic dye paste and Reactive dye.
Method
Preparation of citrus fruit peel: Citrus fruit peels were collected from juice industries. Ripened peels are sorted by identifying with their color; orange color peels are ripened, the peels are washed, dried and grinded into pieces.Pectin extraction and conversion in to sodium pectate: 250 ml water was measured into a 500ml beaker and heated to 50oC. 25 gm milled citrus peel was added to the water. Measured amounts of acid added to the peel-water mixture trace by trace until the desired PH obtained. The mixture was agitated at a constant temperature until the desired extraction time elapsed. Using polyester fabric filter the solid residue of citrus fruit was removed. The filtered solution is collected and approximately the same the volume of solvent added for overnight precipitation. Extraction of pectin Using Na2CO3 was carried out at 50oC with the same procedure followed in acid hydrolysis but 500ml water and 50gm citrus peel was used in a bigger beaker. The precipitate pectin is removed and pectin is reacted with caustic soda and solidified by common salt [10-15]. The solidified sodium pectate is dried in oven dryer at 50oc overnight and ground in small plastic containers.
Printing and testing: Two Fabric samples were printed using sodium pectate and sodium alginate as thickener. The Reactive printed samples are tested for their color strength, wash fastness and hand feels. Relative to the characterized properties the thickeners; alginate thickener and sodium pectate thickeners were compared.
Result and Discussion
Table 1: Keeping the other parameters constant, only extraction time is varied to 1hr, 1hr and 30 minutes and 2 hrs and using acetone to precipitate pectin.



Table 4:


Effect of pH
The effect of pH on extracted pectin yield was determined by adding trace of HCL to alter the pH to the desired values of 1.6, 2.6, and 3.6. Because of slight changes in solution pH throughout the extraction, it was difficult to repeatedly reach an exact pH so approximately 2% error was allowed when measuring pH. The three experiments showed that pectin yield was 23.2% at pH 2.6. The hydrolysis of pectin is facilitated in soften peels. Lower pH, i.e., more strong acid, dissolves the citrus peels [15,16]. The dissolved peels form a thick paste of citrus peel. Pectin is entrapped in the thick paste instead of dispersing through the filter solution. Less pectin amount in the filter solution minimized the amount of precipitated and extracted pectin. Increased pH above 2.6 result in less softness of peels which result in less pectin wash off from the peels, as a consequence less pectin yield.Effect of Extraction Time
The noticeable trend occurred with increasing extraction time from 1 hour to 1:5 hour shows increase in pectin yield. Increasing the extraction time further may result in pectin loss. Accordingly when extraction time is increased from 1.5 to 2 hours the yield of pectin. Flowing of pectin into extraction solution increase as extraction time increases up to 1hr and half. Heating the mixture of peels and water-acid mixture more than 1hr and half will dissolve peels instead of softening and minimize the pectin yield.Effect of Temperature
With increasing extraction temperature up to 65oC pectin yield will increase. Increasing the extraction temperature further result in pectin loss. When extraction Temperature is increased above 65oC the yield of pectin will be minimized. Wash-off of pectin into extraction solution increase as extraction time increases up to 650C after which the yield starts declining. Heating the mixture of peels and water-acid mixture above 65oC will dissolve peels instead of softening and minimize the pectin yield.Extraction of Pectin using Na2CO3
Extraction with Na2CO3 has some advantages than acid hydrolysis of pectin from citrus fruit peel. Extraction carried out using Na2CO3 hydrolyzing agent has yielded more pectin. It is also environment friendly compared to acid hydrolysis. Na2CO3 extracted pectin has improved solubility compared to acid hydrolyzed pectin due to the presence of sodium ion which may give solubility for the extract.Conversion of the Extracted Pectin into Sodium Pectate
The isolated precipitate of pectin which is very slightly gummy and somewhat rubbery was grounded to fine powder and the added to a mixture of 50% isopropyl alcohol and NaOH in solution and then stirred every 5 minutes at room temperature until it creates viscose solution. Finally sodium pectate is formed after which it was filtered to remove excess liquid and washed with water followed by isopropyl alcohol wash to remove excess alkali [17-20]. The pectate may be hydrated during water wash and it must be given consideration to not cause so. Then the dried pectate was solidified with common salt and made ready to serve as printing thickener.Printing Fabric Samples and Testing Printed Fabrics Performance
Evaluation of printing performance was carried out in terms of color strength, wash fastness, rubbing fastness and fabric feel. Two printed fabric samples, one sample (S1) printed by commercial sodium alginate and the other one (S2) with the derived sodium pectate. The recipes for the samples were (as shown in Tables 6 &7):Table 6: Stock Paste Recipe.
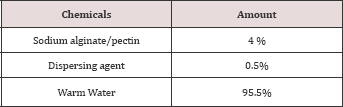

-
a) Prepare printing paste: The paste should be as uniform as
possible. For uniform mix prepare the printing the recipe for stock
paste (as shown in Table 1) was mixed for 5 min at maximum speed. Then
mix the components for printing paste recipe as shown in the Table 2.
The actual quantity of water was to vbe determined practically.
Viscosity should be in such a way that the paste should flow easily
while printing but maintaining the sharpness of the images to be
printed. Two printing pastes were prepared for alginate thickener and
pectin separately.
Figure 1: Printed fabric Samples a) Printed with sodium alginate (S1) b) printed with the derived Sodium Pectate (S2).
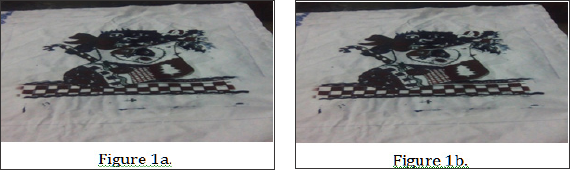
c) Drying: Then the samples were dried at 60oC for 3 min and cure at 150oC for 5 min.
d) Printing performances: Of the printed samples were measured in terms of Color strength, wash fastness, handle feel and rubbing fastness. Color yield of each of the samples was measured using Data color 650 TM spectrophotometer and wash fastness was assessed using laundry meter. For assessing the performance of the two thickeners in terms of wash fatness gray scale and gray staining was done. Accordingly printing performance of the thickeners along with the obtained result is concluded in the following (Table 8).

Table 9: Performance in terms of Color Strength (k/s).
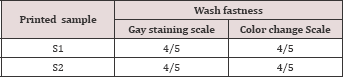
Conclusion
The conversion of pectin into sodium pectate by reacting pectin with caustic soda in isopropyl alcohol must be controlled and given concentration for the production of high quality pectate thickener. Since the derived sodium pectate is washed with water and then with isopropyl alcohol for the production more pure pectate, care must be given during water washing to not hydrate the derived pectate. Solidification of the pectate is done by using common salt.
Sodium pectate thickener printed fabric sample has absorbed more dye than sodium alginate thickener printed fabric sample. The lower reflectance and k/s value has recorded for fabric sample printed with the derived sodium pectate. Even though the difference is neglect able; this truth justified that sodium pectate is more inert thickener than alginate thickener. That is the suspect behind more color strong of sodium pectate. Both alginate and pectate printed samples have very good wash fastness. Since the printing is reactive printing then the attachment of the dyes to the fibers are by covalent bond.
Generally speaking; citrus fruit peels can be used for the production of reactive printing thickeners by acid hydrolysis, using sodium carbonate to hydrolyze pectin in citrus fruits, or other extraction techniques. First pectin is extracted then pectin is reacted with caustic soda forming crude sodium pectate. The crude sodium pectate is then washed in water and in isopropyl alcohol successively to increase the purity of the pectate. The derived sodium pectate is used as textile printing thickener for reactive printing in the same manner alginate is used.
For more Lupine Publishers Open Access Journals Please visit our website:
Follow on Linkedin : https://www.linkedin.com/company/lupinepublishers
Follow on Twitter : https://twitter.com/lupine_online
For more fashion and textile research journal articles Please Click Here:
To Know More About Open Access Publishers Please Click on Lupine Publishers
Follow on Linkedin : https://www.linkedin.com/company/lupinepublishers
Follow on Twitter : https://twitter.com/lupine_online
No comments:
Post a Comment
Note: only a member of this blog may post a comment.